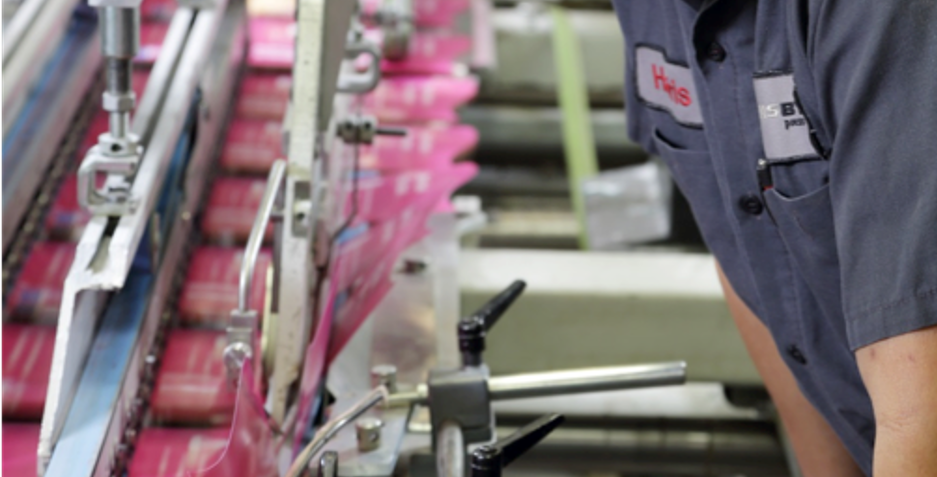
When it comes to creating standout packaging, the folding and gluing process is the unsung hero that transforms flat, printed materials into eye-catching, functional packages. Whether it’s for beauty, wellness, spirits, or consumer goods, precision in folding and gluing can make all the difference in how packaging performs on the shelf. Here are five essential insights into this critical step in the packaging process!
-
More Than Just Folds: The Art of Precision
The folding and gluing process might sound straightforward, but it’s a highly engineered dance of precision, speed, and strength. Each carton undergoes a complex series of folds and adhesive application to ensure structural integrity. Precision is key—any misalignment could compromise the strength and presentation of the package, which is why our equipment and operators are tuned to achieve accuracy down to the millimeter.
-
Speed and Efficiency with High-Tech Automation
Did you know high-speed folding and gluing lines can process tens of thousands of cartons per hour? JohnsByrne’s state-of-the-art machines are designed for efficiency without sacrificing quality. With advanced automation, we can tackle high-volume orders swiftly, helping brands meet tight deadlines and seasonal demands without breaking a sweat. And our careful setup process ensures consistent results across every single unit.
-
Choosing the Right Adhesive Makes All the Difference
From secure retail-ready packaging to intricate promotional pieces, each packaging type may require a unique adhesive. Cold glue, hot-melt, or specialty adhesives are chosen based on material, product weight, and environmental factors. We evaluate all these to ensure the final product can withstand handling, shipping, and display—keeping your product safe and looking its best from start to finish.
-
Structural Complexity, Simplified
Have a unique packaging idea? With folding and gluing, creativity knows no bounds. Our capabilities allow for a variety of structural designs, from classic folding cartons to complex multi-panel configurations. Whether it’s a custom shape, an interactive element, or a high-impact direct mail piece, we bring complex designs to life while ensuring they’re structurally sound and easy to assemble.
-
Quality Control at Every Step
Every package undergoes a rigorous quality control process to meet our high standards. From precise alignment and adhesive application to durability checks, we make sure your packaging not only looks great but performs well. And our technology assists in monitoring for consistency, so each carton is crafted to perfection, ensuring brand integrity and customer satisfaction.
-
Windowing: Showcasing What’s Inside
Windowing is a valuable feature that adds transparency, literally and figuratively, to your packaging. By incorporating a clear, durable window within the carton, consumers can catch a glimpse of the product inside, which builds anticipation and drives purchase decisions. Commonly used in industries like beauty, wellness, and specialty foods, windowing requires precision in both material choice and placement to ensure durability while keeping the product secure.
At JohnsByrne, our folding and gluing process includes precision windowing options that fit seamlessly into the design. Whether for a small peek at the product or a larger display panel, our windowing applications balance visibility and protection, providing an elegant solution for showcasing products without compromising packaging integrity.
Ready to Bring Your Packaging Vision to Life?
At JohnsByrne, our folding and gluing capabilities ensure that every package we produce not only meets but exceeds your standards. Whether you’re launching a new product, preparing for a special promotion, or simply looking to elevate your brand’s packaging, we’re here to help make it happen with precision, speed, and creativity.
Learn more about our streamlined finishing capabilities: https://www.johnsbyrne.com/why-jb/finishing/
Explore the possibilities with us today and discover how JohnsByrne’s folding and gluing expertise can bring your next packaging project to life!
Related Posts
In today’s competitive market, packaging does more than just protect a product; it tells a story, engages the senses, and leaves a lasting impression on … 20 Premium Packaging Finishes: A Guide to Elevating Your Brand Experience
This is simple: it’s not just a box. Every product deserves packaging that is both practical and exceptionally appealing. It should be structurally conceived so … Custom Product Packaging Solutions for Brand Loyalty and Preference
As a leading provider of premium packaging and custom print solutions to the Beauty & Wellness, Spirits, Financial Services, Consumer Products and Entertainment markets, JohnsByrne … Elevating Brands Through Advanced Digital Enhancement